Some Of Crossdock Warehouse
Wiki Article
An Unbiased View of Sacramento Crossdock Warehousing
Table of ContentsFacts About Crossdock Warehouse RevealedHow Crossdock Warehouse can Save You Time, Stress, and Money.Sacramento Crossdock for BeginnersThe Basic Principles Of Sacramento Cross Dock Crossdock Warehouse Fundamentals Explained
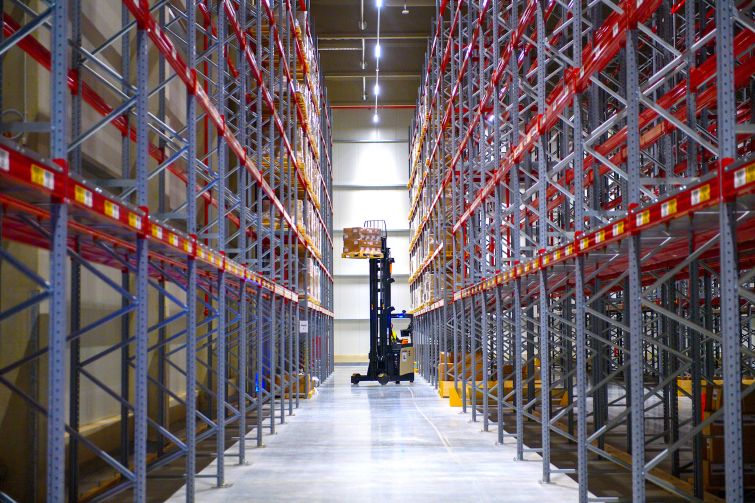
As a part of SCM, effective inventory management might lead to a more powerful supply chain. Another reason great warehousing is important to SCM is that it offers a means for services to make certain the availability of the best items at the appropriate area whenever the time is. It boosts the utility value of the items this way - Sacramento Warehouse.
Customers anticipate to understand when roughly their purchases will be delivered after an order is placed. The knowledge pertaining to the distribution time enhances their self-confidence. Several of them pay much faster as a result. Certainly, they end up being much more hesitant when uncertainty exists around the prompt shipment of products. Nowadays, distribution rate appears to be one of the substantial aspects that consumers consider when choosing an item and also making a decision whether or not to proceed with the acquisition.
What Does Sacramento Crossdock Do?
A significant reason to invest in constructing a warehouse is the several recognized financial advantages that feature it. Not just the enhanced efficiency of the supply chain but additionally the stockroom's storage space ability and just how it works as a central area for your products add to its economic advantages.These things might be seen or know with loan consolidation and build-up procedures. Below's a closer consider just how consolidation and also buildup might aid reduced prices: With combination procedures, there's no requirement to ship items independently from numerous sources due to the fact that they could be supplied to your stockroom as supplies. When an order is put, you or your personnel can load as well as ship the product out from there.
Not just that, but excellent warehousing additionally improves customer support as well as provides economic benefits. Every one of these points might lead to higher profits and enhanced business earnings.
Not known Details About Sacramento Cross Dock
Delivering supplies for order satisfaction. People that pack products right into a warehouse and others ("pickers") that fill orders in a real warehouse, plus those that manage the facility and also procedure. Protection to secure stored products. Accessibility to cost-efficient transportation to bring products in or move them out as orders are fulfilled.They additionally need to make certain that items are saved in a safe and secure fashion. Warehouse examples consist of retail shops, circulation facilities, cold store facilities, and also manufacturing plants. In retail shops, things are saved as well as organized in a stockroom as well as delivered to consumers or other shops. Warehouse are made use of to shop and distribute items to several areas.
Warehousing best technique is to utilize RF Scanners, or equivalent innovations, to additional boost stock accuracy and also live stock tracking. Closely intertwined with Receiving, Putaway is the final stage of incoming handling. Putaway is the procedure of literally, and also methodically, putting products into their appropriate final storage space places (Sacramento Cross Dock). Team chooses Item check my reference to putaway from Putaway Hosting area, Generally Pallets or Carts with Product all set to be putaway, Making use of RF Scanner, identify what cart/pallet/job you are placing away and check one-of-a-kind identifier to start Putaway, Picker takes a trip to area to place product for storage space, Ideal ideal in course systems inform personnel where to position item, but lots of storehouses still have staff location product where they know there is void (with some standards applied)RF Check Item being putaway as well as Place where the Item is putaway, Continue process (most likely to location and also place supply) until entire order, pallet, cart, etc is complete Weight and dimensions of product/pallet being putaway, Stowability of Item (ie delicate, stackable, and so on)Deal quantity (HOT things positioned close vs NOT far away)Amount got, Value of product, Pick Sort of Product (solitary pick, set pick, collection choice, area choice, etc) Accurate Putaway is vital in the warehouse operation, ensuring that Item can be quickly located specifically when it is needed.
The Definitive Guide for Sacramento Cross Dock
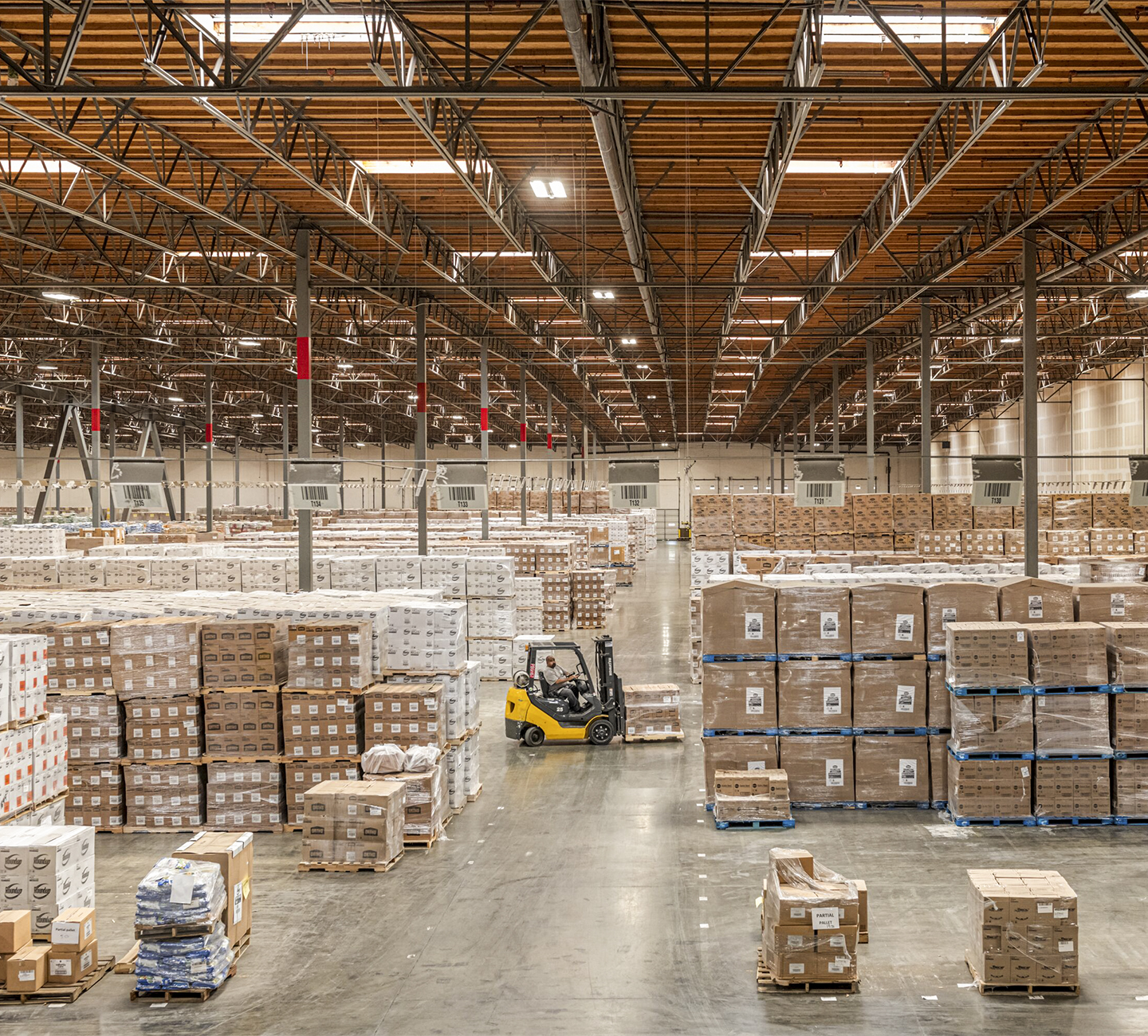
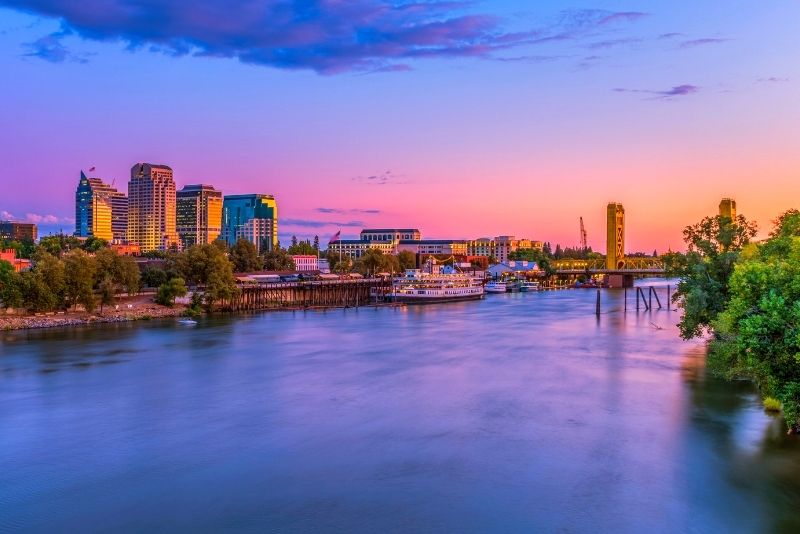
Similar to exactly how Getting lays the foundation for an exact supply, Selecting lays the structure to precisely accomplish a client's order. Choosing is the process of celebration Products to accomplish a customer's order demand. Picker is designated Select(s)There are numerous choose approaches, each operation is one-of-a-kind in what is most effective for their demands, Zone selecting, batch picking, single order picking, wave picking, and a lot more, Utilizing RF Scanner, or similar, begin selecting by getting in the Distinct Choose Identifier (batch #, Order #, SO #, Choose #, various other recommendation)Picker is directed with the Select Course (ideally based on optimization logic) to satisfy the Select, scanning Products and Locations as they proceed, Chosen items might be positioned in totes, pallets, carts, shelf, etc during choice, Completely selected orders provided to next stage of procedure, Picked orders may be supplied to a Quality assurance area, Packing/Shipping location, or straight to outbound hosting (if choice to label procedure) relying on operation Limitations/abilities of present Warehouse Monitoring System (WMS)Quantity of Orders # of Item Lines per Order, Kind of storage media (shelving vs racking vs ground pallet storage space)What the Packaging and also Shipping Refine resembles (carefully linked to Selecting)Item need added attention during packing? Transport Management System (TMS) efficient in supplying delivery tags before things are picked? A lot more! Stockroom Design Picking should be done properly, with top quality control steps in place post-picking, to achieve consumer order satisfaction precision near 100%.
So if throughout shipping the weight is not within the defined resistance range, then the individual will certainly be triggered to do something about it, Dimension tolerance check throughout Shipping, Similar to read what he said Weight resistance based on system dimension information Packaging as well as Shipping is a major emphasis of warehouses, as it typically becomes a traffic jam since Order Processing Time must be as brief as possible to meet client assumptions.
Do NOT sacrifice quality! You can assure the inventory at the storage facility visit this site is accurate and updated with a well specified Stock Control procedure.
Rumored Buzz on Sacramento Crossdock
Cycle Counts and Complete Supply Counts are tools related to keeping Supply Control. Cycle Matters occur continually while typical procedures proceed, however Complete Supply Counts happen occasionally and need all product motion to discontinue up until a complete accurate count is completed. Shutdown all inventory movements, completing all Item Activities in the Stockroom (literally and also methodically)Make certain all inbound as well as outgoing orders that have actually been physically refined, have likewise been processed in WMSBreak storehouse group right into groups to count (in some cases 1 person group all right)Groups are designated areas to count Assign small-medium locations to count, after that teams check in for even more areas as required, Groups count appointed locations, taping counts of product per location, Teams often utilizing RF Scanners to record matters, Or else have to do paper-based which is difficult to achieve a Blind Count, Group reports back once completed and also get next Count Task, After areas are Counted, the Manager/Lead assesses all Variations, Manager designates various Team to recount the distressed Products and/or Locations, If 2nd group counts very same as first team, make inventory change to match physical count.Report this wiki page